Industrial Wood Chipper: Your Ultimate Guide
Welcome to My Blog!
Before we dive into the content, I’d love for you to join me on my social media platforms where I share more insights, engage with the community, and post updates. Here’s how you can connect with me:
Facebook:https://www.facebook.com/profile.php?id=61557298070472
Now, let’s get started on our journey together. I hope you find the content here insightful, engaging, and valuable.
Introduction
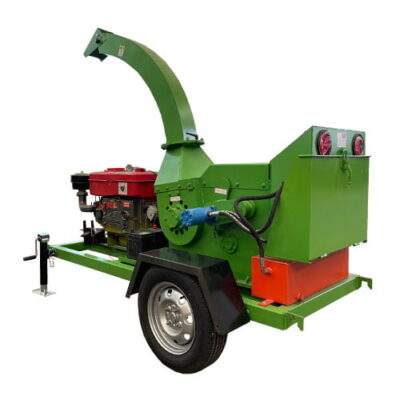
An industrial wood chipper is a powerful, versatile machine designed to efficiently reduce large pieces of wood into smaller, more manageable wood chips. These machines are indispensable tools in various industries, including forestry, landscaping, agriculture, and manufacturing. The wood chips produced by these machines have a wide range of applications, such as mulch for landscaping, fuel for biomass power plants, and raw material for paper production.
In this comprehensive guide, we will delve deep into the world of industrial wood chippers. We will explore the different types of wood chippers available, their working principles, their diverse applications, and the key factors to consider when purchasing an industrial wood chipper. We will also discuss important safety precautions and maintenance tips to ensure optimal performance and longevity.
Types of Industrial Wood Chippers
Industrial wood chippers can be categorized based on their feeding mechanism, cutting method, and mobility.
Drum-type chippers:
- These chippers utilize a rotating drum equipped with sharp knives to cut the wood.
- They are highly efficient and capable of handling a wide range of wood sizes, making them suitable for large-scale operations.
- Drum-type chippers are often used in forestry and timber processing industries.
Disc-type chippers:
- Disc-type chippers feature a rotating disc with sharp blades that cut the wood as it passes through.
- They are typically used for smaller wood pieces and are more portable than drum-type chippers.
- Disc-type chippers are commonly used in landscaping and gardening applications.
Hammermill chippers:
- Hammermill chippers employ a rotating drum with hammers that strike the wood, breaking it down into smaller pieces.
- They are well-suited for processing woody materials with high moisture content, such as green waste and agricultural residues.
- Hammermill chippers are often used in composting and biomass production.
Working Principle of an Industrial Wood Chipper
The working principle of an industrial wood chipper is relatively straightforward. The wood is fed into the machine, where it is securely held in place by a feed roller. A rotating cutting element, such as a drum or disc, then cuts the wood into smaller pieces. The size of the wood chips can be adjusted by modifying the spacing of the knives or the speed of the cutting element.
Applications of Industrial Wood Chippers
Industrial wood chippers have a wide range of applications across various industries:
Forestry:
- Clearing land of debris and undergrowth.
- Preparing wood for pulp mills and other wood processing facilities.
- Reducing the risk of wildfires by creating fuel breaks.
Landscaping:
- Producing high-quality mulch for gardens, parks, and landscaping projects.
- Recycling yard waste and green waste into valuable mulch.
Agriculture:
- Processing agricultural waste, such as tree branches, cornstalks, and other woody materials.
- Creating biomass fuel for power generation and heating.
Manufacturing:
- Providing raw material for paper production, particleboard, and other wood-based products.
- Supplying wood chips for industrial processes, such as boiler fuel and chemical production.
Factors to Consider When Purchasing an Industrial Wood Chipper
When purchasing an industrial wood chipper, several key factors should be carefully considered:
Capacity:
- The amount of wood the machine can process per hour.
- This is crucial for determining the machine’s suitability for your specific needs.
Feed size:
- The maximum size of wood that can be fed into the machine.
- Consider the types of wood you will be processing and choose a machine with an appropriate feed size.
Mobility:
- Whether the machine is stationary or portable.
- A portable chipper offers greater flexibility, while a stationary chipper may be more powerful and efficient.
Power source:
- Electric, diesel, or gasoline.
- Choose a power source that is reliable, cost-effective, and suitable for your operating environment.
Safety features:
- Emergency stop buttons, guards, and other safety devices.
- Prioritize safety by selecting a machine with robust safety features to protect operators and bystanders.
Maintenance of Industrial Wood Chippers
Proper maintenance is essential for ensuring the longevity and optimal performance of an industrial wood chipper. Regular maintenance tasks include:
Cleaning:
- Remove debris and wood chips from the cutting chamber, feed rollers, and other components.
- Regular cleaning prevents buildup and ensures efficient operation.
Lubrication:
- Apply grease or oil to moving parts, such as bearings, gears, and chains.
- Proper lubrication reduces friction and extends the life of the machine.
Inspection:
- Check for wear and tear on knives, belts, and other components.
- Early detection of potential problems can prevent costly repairs.
Sharpening:
- Sharpen the knives regularly to maintain cutting efficiency.
- Dull knives can lead to reduced performance and increased power consumption.
Safety Precautions When Operating an Industrial Wood Chipper
Industrial wood chippers can be dangerous if not operated safely. It is crucial to follow these safety precautions:
Wear protective gear:
- Safety glasses, gloves, hearing protection, and sturdy footwear are essential.
- Proper protective gear minimizes the risk of injury.
Clear the work area:
- Remove any debris, obstacles, or loose clothing that could get caught in the machine.
- A clear work area reduces the risk of accidents.
Never feed wood into the machine while it is running.
- Always wait for the machine to come to a complete stop before feeding wood.
- This prevents the risk of injury from flying debris.
Use a push stick to feed wood into the machine.
- A push stick keeps your hands away from the cutting elements.
- This is a crucial safety measure to avoid accidents.
Comparison of Different Types of Industrial Wood Chippers
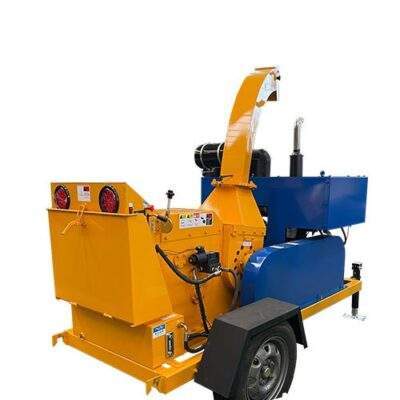
Feature | Drum-type Chipper | Disc-type Chipper | Hammermill Chipper |
---|---|---|---|
Capacity | High | Medium | High |
Feed size | Large | Small to medium | Small |
Mobility | Stationary | Portable | Portable |
Applications | Forestry, landscaping | Landscaping, agriculture | Agriculture, manufacturing |
Conclusion
Industrial wood chippers are powerful and versatile machines that play a crucial role in various industries. By understanding the different types of wood chippers, their working principles, and the factors to consider when purchasing one, you can make an informed decision and select the right machine for your specific needs. Remember, safety should always be a top priority when operating an industrial wood chipper.
FAQ
What is the difference between a wood chipper and a wood shredder?
A wood chipper produces larger, more uniform wood chips, while a wood shredder creates smaller, more irregular wood chips or mulch.
How do I choose the right size wood chipper for my needs?
Consider the types of wood you’ll process, the volume of material, and the desired chip size. Consult with a professional or refer to the manufacturer’s specifications.
What is the best way to dispose of wood chips?
Wood chips can be used for various purposes, such as mulch, compost, or biomass fuel. Consult local regulations for proper disposal methods.
How often should I sharpen the knives on my wood chipper?
The frequency of sharpening depends on usage and the type of wood being processed. As a general rule, sharpen the knives every 20-30 hours of operation.
What are the safety regulations for operating an industrial wood chipper?
Always follow the manufacturer’s safety guidelines and local regulations. Wear appropriate protective gear, clear the work area, and never feed wood into the machine while it’s running.